
Strive to build the company into a decorative fabric and clothing fabric dyeing and finishing processing enterprise that practices the concept of green development
Shaoxing Nanyang Dyeing and Weaving Co., Ltd. was founded in 1982 and is a professional enterprise engaged in the dyeing and finishing of decorative fabrics and clothing fabrics. In order to actively respond to the government's call to enhance the competitive advantage of the textile industry, promote industrial economic transformation and upgrading, while controlling quantity and improving quality, energy conservation and emission reduction, a contract was signed in 2011 to gather in the Binhai Industrial Zone. In early 2016, the entire area was relocated to the Binhai Industrial Zone.
The enterprise currently covers an area of 102 acres, employs 1200 people, and has a total project investment of 400 million yuan. The company has six workshops specializing in the dyeing and finishing of decorative and clothing fabrics. It has excellent dyeing and finishing equipment, and has an annual production capacity of 450 million meters for dyeing and finishing various types of fabrics.
According to the concept of building a green printing and dyeing cluster proposed by Keqiao District, the company has closely focused on energy conservation and environmental protection during the project implementation process, and carried out transformation and upgrading in the following aspects:
1. Device upgrade:
Taking advantage of the opportunity of gathering and relocating, the company has upgraded its equipment, eliminated outdated equipment, introduced low bath ratio gas (liquid) flow dyeing machines, and also introduced continuous pre-treatment equipment. All the molding machines introduced by South Korean companies Lihe and Nissin adopt medium pressure steam heating, greatly improving energy utilization efficiency.
2. Process improvement:
The company actively cooperates with research institutes of universities and colleges to improve the original traditional process, adopting a one bath method and short process process, greatly reducing the use of additives and dyes, not only reducing production costs, but also greatly reducing pollutant emissions, enhancing the company's competitiveness in the market.
3. Management improvement:
At the beginning of the gathering, the company collaborated with relevant units to develop an ERP management system that is suitable for the actual situation of the company. Our company's ERP system achieves refined management from aspects such as workshop operation management, formula management, quality management, cost management, sales management, dyeing and chemical material management, grey fabric and finished product management, accounts payable and accounts receivable management, achieving standardization, informatization, and automation, improving the management level and product quality of the enterprise, and reducing production costs.
For many years, the company has been focusing on enterprise management, technological progress, and talent cultivation, adhering to the factory policy of "quality first, reputation first". And pay attention to environmental protection construction, strive to do a good job in environmental protection work, and strive to "clear water and blue sky".
Facing the future, we will continue to make efforts, further deepen reforms, develop new products, strengthen internal management, further save energy and reduce consumption, tap into internal potential, seize opportunities, actively strive for progress, and create greater brilliance with excellent quality, serious management, enthusiastic service, good performance, and the spirit of "unity, dedication, progress, and pragmatism".
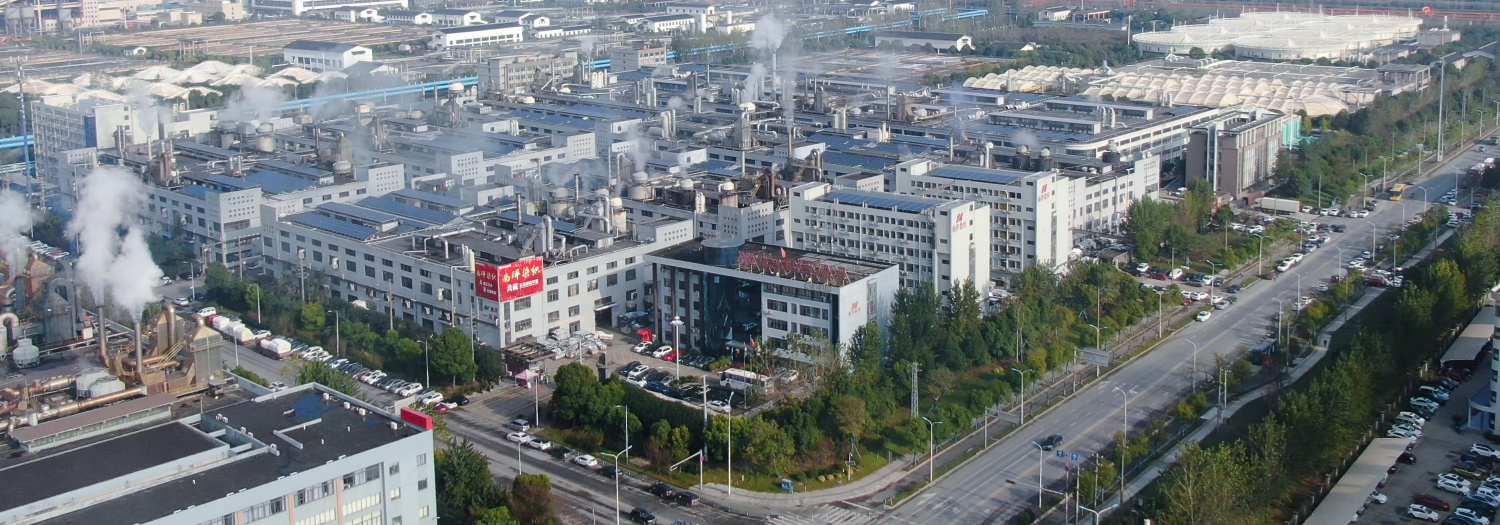